Ensuring the integrity and success of drilling and cementing operations is paramount in the construction, mining, and tunneling industries. A critical component in achieving this is the humble yet vital casing centralizer. This guide dives deep into the world of centralizers, exploring different types like solid rigid centralizers, spiralizer centralizers, and roller centralizers. Understanding these components is crucial for procurement professionals like you, Mark, who need reliable, high-quality equipment that performs under pressure. We'll cover everything from basic functions to specific designs like the spiral vane solid rigid centralizer and heavy duty welded positive spiralizer, helping you make informed decisions for your projects. This article is worth reading because getting centralization right prevents costly cementing failures and ensures wellbore integrity, directly impacting project timelines and budgets.
What Exactly is a Casing Centralizer and Why is it Essential?
At its core, a casing centralizer is a mechanical device secured around the casing string used in oil, gas, water well drilling, and geotechnical applications. Its primary function is deceptively simple but fundamentally important: to keep the casing centered within the wellbore (either an open hole or a larger casing). Why is this centering action so critical? It ensures a uniform annular space between the casing and the borehole wall. This uniformity is vital for achieving a successful cement job.
Imagine trying to pour cement evenly into a gap where the pipe is leaning against one side. You'd end up with a thick layer of cement on one side and a very thin, potentially non-existent layer on the other. This uneven distribution compromises the seal, potentially leading to fluid migration, poor zonal isolation, and ultimately, well integrity issues. A properly placed centralizer prevents this by maintaining standoff, allowing the cement slurry to flow completely around the casing. This creates a strong, consistent sheath that supports the casing, isolates different geological zones, and protects the casing from corrosion. The centralizer helps ensure the long-term stability and safety of the well.
Furthermore, centralizers play a role during the running of the casing itself. They reduce the force needed to run the casing (running force) by minimizing the contact area between the casing and the borehole wall, thus reducing friction. This is especially important in highly deviated or horizontal wells, where gravity works against you. Using the right centralizer can prevent the casing from getting stuck and ensure it reaches the target depth efficiently. Neglecting proper centralization can lead to expensive remedial cementing operations or even compromise the entire project.
How Do Different Centralizer Types Compare? Solid Rigid vs. Spiral Vane vs. Roller Centralizers
The world of centralizers isn't one-size-fits-all. Different well conditions and operational requirements demand different types of centralizers. Broadly, they fall into a few main categories, each with unique characteristics. Understanding these differences is key to selecting the most effective and cost-efficient solution for your specific application. Let's compare three common types: solid rigid centralizers, spiral vane centralizers (often a type of spiralizer centralizer), and roller centralizers.
Feature | Solid Rigid Centralizer | Spiral Vane Centralizer | Roller Centralizer |
---|---|---|---|
Construction | Solid, non-flexible body (often cast or welded steel) | Features spiral vanes or blades | Incorporates rollers on the outer body |
Flexibility | None (Rigid) | None (Rigid) | None (Rigid Body, but rollers rotate) |
Standoff | High, positive standoff | Good standoff, promotes fluid swirl | High standoff, reduces rotational friction |
Friction | Higher drag | Moderate drag, aids mud removal | Very low rotational friction / drag |
Application | Vertical/low deviation wells, where high standoff is key | Deviated/Horizontal wells, good mud removal | Highly deviated/horizontal wells, tight tolerances |
Key Benefit | Maximum strength, reliable standoff | Improved cement displacement, hole cleaning | Minimizes torque and drag during rotation |
Solid rigid centralizers provide the highest restoring force (the force pushing the casing back to the center) and are excellent for ensuring standoff in less complex well paths. However, their rigidity can lead to higher drag forces. Spiral vane centralizers, a type of spiralizer, are specially designed with blades that wrap around the casing. These spiral vanes induce a swirling motion in the fluid during cementing, which helps to displace drilling mud more effectively, leading to a better cement bond. They offer a good balance between standoff and improved fluid dynamics. Roller centralizers are engineered for the most challenging conditions, particularly highly deviated and horizontal wells. The rollers significantly reduce torque and drag when rotating or running the casing, making operations smoother and reducing the risk of getting stuck. Choosing between them depends heavily on the well trajectory, hole conditions, and cementing requirements.
What Makes a Solid Rigid Centralizer the Right Choice for Certain Applications?
A solid rigid centralizer is characterized by its robust, non-flexible construction. These centralizers are typically made from cast iron, steel, or sometimes even specialized alloys, ensuring high strength and durability. Their primary advantage lies in providing a guaranteed, positive standoff. Unlike bow spring centralizers (another common type not detailed here), rigid centralizers do not flex under load. This means that if the annular space is tighter than the centralizer's outer diameter, the centralizer won't simply collapse; it will maintain its shape and centering function, albeit with increased force required to run the casing.
This positive standoff capability makes the solid rigid centralizer an excellent choice in situations where maintaining a specific minimum annular space is critical for the cement job, especially in vertical or near-vertical wells where running forces are less of a concern. They are often preferred in larger diameter casing applications where the weight and stiffness of the casing string demand substantial support. The construction of a solid rigid centralizer, often involving heavy steel, ensures it can withstand significant axial and radial loads encountered during casing running and cementing operations.
However, their rigidity means they generate higher drag forces compared to other types, especially in deviated sections. Therefore, their use might be limited in wells with significant doglegs (sharp turns) or long horizontal sections where minimizing friction is paramount. They are also ideal when the borehole is relatively smooth and gauge (meaning the diameter is consistent). For procurement professionals like Mark, sourcing high-quality solid rigid centralizers means looking for consistent casting or weld quality and adherence to material specifications to ensure reliable performance and durability. These are foundational tools in many standard drilling operations.
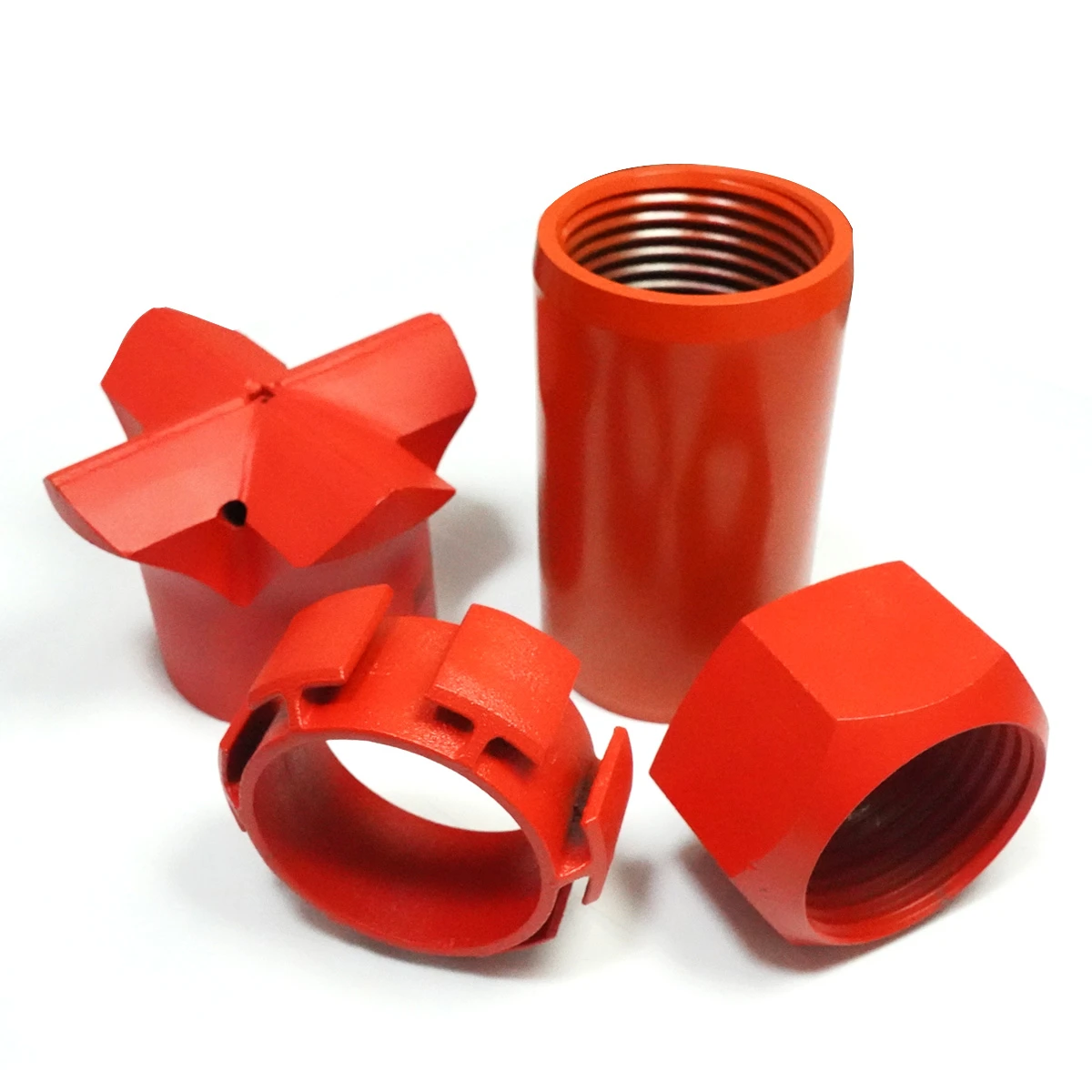
When Should You Use a Spiralizer Centralizer? Exploring Spiral Vane Designs
The spiralizer centralizer, often featuring spiral vanes, represents an evolution designed to enhance cementing efficiency, particularly in wells that aren't perfectly vertical. The defining feature is the set of helical blades or vanes attached to the centralizer body. These spiral vanes serve multiple crucial functions beyond just centering the casing. As the casing is run into the hole and during the circulation and cementing process, the spiral vane design imparts a swirling or rotational motion to the fluids in the annulus.
This induced turbulence is highly beneficial. It helps to effectively dislodge and remove pockets of drilling mud and filter cake that might otherwise remain stuck to the borehole wall. Complete mud removal is essential for achieving a strong, long-lasting bond between the cement and both the casing and the formation. Think of it like using a scrub brush versus just rinsing – the spiral action cleans the annulus more thoroughly. The spiralizer is designed especially for this purpose, improving cement displacement efficiency significantly.
Spiralizer centralizers, including spiralizers with pronounced spiral vanes, are particularly well-suited for deviated and horizontal wells. While they are rigid and provide positive standoff like standard solid rigid centralizers, their design offers lower flow restriction compared to solid-body types, allowing cement slurry to pass more easily. The wide symmetrical spiral fins contribute to robust standoff while promoting 360-degree cement coverage. When choosing a spiralizer centralizer, factors like vane height, angle, and the number of vanes should be considered based on the specific well geometry and fluid properties. They represent a smart choice when improving cement integrity is a high priority.
Why are Spiral Vane Solid Rigid Centralizers Popular in Demanding Wells?
The spiral vane solid rigid centralizer combines the best attributes of both the solid rigid design and the spiral vane concept. These centralizers are built for toughness and optimized performance in challenging downhole environments, particularly highly deviated horizontal wells. They feature a solid, rigid body, ensuring maximum structural integrity and reliable positive standoff, just like a standard solid rigid centralizer. This heavy steel construction is highly effective in supporting the casing weight and resisting compression forces.
Layered onto this robust frame are the spiral vanes. As discussed, these vanes are specially designed to promote fluid turbulence, significantly enhancing mud removal and ensuring uniform cement distribution around the casing. This combination is powerful: you get the uncompromising standoff of a rigid centralizer along with the superior cementing efficiency of a spiralizer. The welded spiral vane solid rigid construction ensures the vanes are securely attached and can withstand the rigors of running casing in complex well paths. Symmetrical spiral fins are welded to the body, providing strength and consistent performance.
The spiral solid centralizers were developed specifically in response to the need for better cementing in deviated and horizontal sections. In these wells, gravity tends to pull the casing to the low side of the hole, making centralization difficult and often leading to poor cement jobs. The spiral vane solid rigid centralizer directly addresses this by providing strong mechanical standoff while simultaneously optimizing the hydraulics of cement placement. Their robust nature also means they are less susceptible to damage during run-in compared to more flexible designs. For projects involving expensive completions in challenging formations, the reliability offered by a steel spiral vane solid rigid centralizer often justifies the investment.
What are the Advantages of Using Roller Centralizers, Especially Low Drag and Rigid Roller Types?
Roller centralizers represent a specialized category engineered primarily to minimize torque and drag when running and rotating casing strings. This is especially critical in extended-reach drilling (ERD), highly deviated, and long horizontal wells, where cumulative friction forces can become prohibitively high. A roller centralizer features rollers embedded in its outer surface. These rollers allow the centralizer body (and thus the casing) to translate axially (move up or down the hole) with significantly less friction than a standard rigid centralizer that scrapes against the wellbore.
The key advantage is the reduction in rotational torque and running drag. When rotating the casing (sometimes necessary during running or cementing), the rollers turn against the borehole wall, dramatically reducing the force required. This makes it easier to reach target depth, reduces stress on the casing string and the top drive, and minimizes the risk of buckling or excessive wear. Low drag roller centralizers are specifically optimized for this purpose. Some designs, known as rigid roller centralizers, combine the low-friction benefits of rollers with a very strong, solid rigid body structure to ensure reliable standoff even under high loads.
Torque roller centralizers are specially designed for these demanding applications. While often more expensive than standard rigid or spiralizer centralizers, the operational benefits can outweigh the cost in challenging wells. They facilitate smoother operations, reduce potential NPT (non-productive time) associated with high torque and drag, and can enable the successful completion of wells that might otherwise be impossible. The roller centralizer is a complete mechanical solution designed for extended-reach wells. When evaluating roller centralizers, consider the roller material, bearing design, and the overall robustness of the centralizer body to ensure it meets the specific demands of the drilling operation.
How are Slip-On Welded Positive and Heavy Duty Welded Positive Spiralizers Constructed for Durability?
Durability and reliability are paramount, especially when sourcing equipment like centralizers from overseas suppliers. Understanding the construction of types like slip-on welded positive and heavy duty welded positive spiralizers can provide confidence in their performance. These centralizers are typically fabricated from high-quality steel to withstand demanding downhole conditions. The term "slip-on" indicates that the centralizer is designed to slide onto the casing joint and is usually held in place between two stop collars, rather than being directly welded or clamped onto the casing.
The "welded positive" aspect refers to the construction method and performance. The components, such as the end bands and the vanes or bows (in the case of a spiralizer), are securely welded together. This weld process is critical. Reputable manufacturers use controlled welding procedures to ensure strength and uniformity in every weld. This contrasts with non-welded designs, which might rely on interlocking parts or rivets. A good weld ensures the centralizer maintains its structural integrity under high axial loads and impacts encountered during casing running. The "positive" designation implies that it provides a reliable, positive standoff, characteristic of rigid centralizers.
Heavy duty welded positive spiralizers take this a step further. They are built with thicker materials and often feature reinforced weld joints. The heavy duty spiralizer is designed especially for highly deviated horizontal wells or other demanding scenarios involving heavy casing strings or potentially rough borehole conditions. The slip on welded heavy duty design combines ease of installation (slipping onto the casing) with robust construction. Often, these centralizers undergo surface treatments, like a special iron phosphate coating process followed by a special polyester powder coating. This phosphate coating process to prevent corrosion and improve paint adhesion, further enhancing the centralizer's longevity in harsh downhole environments. As Allen from Jiufu, we ensure our welding processes meet stringent quality control standards, providing that ultimate strength and uniformity Mark looks for.
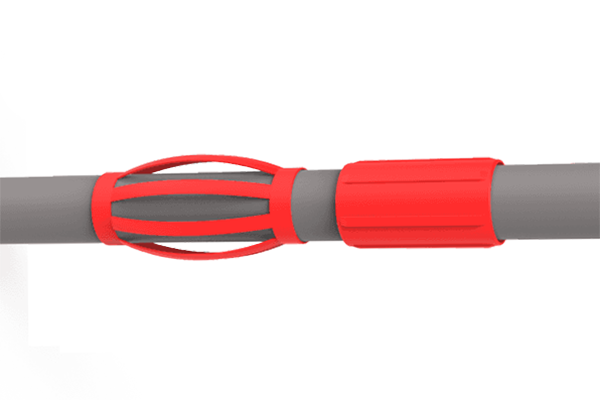
What Role Does the Stand Off Band Play in Casing Centralization?
While full-body centralizers like rigid, spiral, and roller types are common, sometimes a simpler solution called a stand off band is used. A stand off band, also known as a standoff ring, is essentially a solid ring, often made of steel, zinc alloy, or even rigid polymer composite, that is attached around the casing. Its primary function, as the name suggests, is to provide a specific amount of standoff – keeping the casing body away from the wellbore wall.
Unlike more complex centralizers, a stand off band typically doesn't have bows or vanes. It provides standoff through its own thickness. The standoff band is designed to provide a positive, fixed distance between the casing and the borehole. These are often used in situations where only minimal standoff is required, or in close tolerance between the casing and the hole where larger centralizers might not fit or could unduly restrict flow. They can be particularly useful in cased and open holes.
A slip on standoff band is installed similarly to slip-on centralizers, positioned on the casing and secured between stop collars. Their simple, robust design makes them very durable. They are sometimes used in conjunction with other types of centralizers to provide additional support points along the casing string. While they don't offer the flow-enhancing properties of a spiralizer or the friction reduction of a roller centralizer, they are a cost-effective solution for achieving basic standoff requirements in less demanding applications or specific sections of the well. For applications requiring reliable accessories, consider exploring options like high-quality Nuts and Washers to complement your anchoring systems.
How Do Centralizers Perform in Highly Deviated and Horizontal Wells?
The performance of centralizers becomes significantly more critical and complex in highly deviated and horizontal wells. In these trajectories, gravity constantly pulls the casing string towards the low side of the borehole, making effective centralization much harder to achieve than in vertical wells. Insufficient standoff on the low side can lead to a poor cement channel, compromising zonal isolation. Furthermore, the increased contact area between the casing and the wellbore in these wells leads to significantly higher friction (drag) when running the casing and higher torque when rotating it.
This is where specialized centralizer designs truly shine. Standard solid rigid centralizers, while strong, can create excessive drag. Spiralizer centralizers (spiralizers) help by promoting better mud removal, which is often more challenging on the low side of a horizontal hole. Their spiral vane design aids in lifting debris and ensuring cement can flow into that critical low-side space. The centralizer is designed to facilitate this. Welded spiral vane solid rigid types are often preferred here for their combination of strength and flow enhancement. They were developed in response to the need for better cementing in deviated and horizontal sections.
Roller centralizers offer the most significant advantage in reducing torque and drag. In long horizontal sections, the ability to run the casing smoothly to bottom without exceeding the equipment's torque limits or causing buckling is paramount. Low drag roller centralizers and low torque roller centralizers are specifically designed for use in highly deviated wells. Heavy duty versions of spiralizers and roller centralizers are often necessary to withstand the heavy loads in highly deviated horizontal sections. Proper centralizer selection and placement strategy are crucial engineering considerations for the success of any highly deviated horizontal wells.
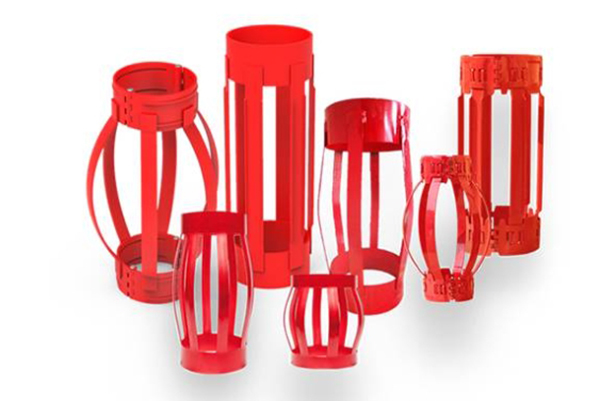
What Key Factors Should Procurement Professionals Consider When Sourcing Centralizers?
For procurement professionals like Mark Davis, sourcing centralizers, especially from international suppliers, involves balancing quality, cost, and reliability. Here are key factors to consider:
- Material Specifications and Quality: Insist on clear specifications for the materials used (e.g., steel grade, casting quality). Request material test reports (MTRs) if necessary. The centralizer must be robust enough for the application. Look for heavy steel construction where strength is needed.
- Weld Integrity (for Welded Types): If sourcing welded centralizers (like slip on welded positive or welded spiral vane solid rigid types), inquire about the welding process and quality control measures. Consistent, high-quality welds are crucial for structural integrity. Look for suppliers who emphasize strength and uniformity in every weld.
- Design Suitability: Ensure the chosen centralizer type (solid rigid, spiralizer, roller, stand off band) matches the well conditions (deviation, hole size, potential obstructions) and operational requirements (cementing strategy, need for rotation). Is a heavy duty spiralizer needed, or will a standard rigid casing centralizer suffice?
- Standoff Performance: The primary job of a centralizer is standoff. Check the manufacturer's stated standoff efficiency or restoring force data. Ensure it meets the project's engineering requirements. Does the band is designed to provide sufficient standoff?
- Coating and Corrosion Protection: Downhole environments can be corrosive. Check if the centralizers have protective coatings (e.g., special iron phosphate coating process, special polyester powder coating) to enhance lifespan.
- Supplier Reliability and Communication: As Mark knows, communication is key. Choose suppliers with responsive sales and technical support. Look for factories like ours with established production lines and a track record of exporting to your region (USA, Europe, Australia). Clear communication avoids misunderstandings about specifications and delivery schedules.
- Certifications and Compliance: While certificate fraud can be a concern, reputable suppliers should be able to provide documentation for quality management systems (like ISO 9001) or adherence to industry standards (like API Spec 10D, though not all centralizers fall under this). Verify claims where possible.
- Logistics and Lead Times: Factor in shipping times and potential delays. A reliable supplier provides realistic lead times and works to meet project deadlines. This is crucial for avoiding the pain point of missed project milestones due to late shipments. Consider the entire system, including necessary components like reliable Couplings which are also vital for project timelines.
- Cost-Effectiveness: While price is important, focus on overall value. A slightly cheaper centralizer that fails downhole or causes operational issues is far more expensive in the long run. Balance upfront cost with quality, durability, and the supplier's reliability.
By carefully evaluating these factors, procurement officers can confidently source high-quality centralizers that contribute to successful and efficient drilling and completion operations. Partnering with a factory direct source like Jiufu, which understands these requirements and prioritizes quality control, can mitigate many common purchasing pain points.
Key Takeaways:
- Centralizers are essential: They ensure proper casing standoff for effective cement jobs and reduce running forces, crucial for well integrity.
- Types vary: Choose based on well conditions: Solid rigid centralizers for strength, spiralizer centralizers (spiral vane) for better cementing, and roller centralizers for low friction in deviated/horizontal wells.
- Construction matters: Look for quality materials, robust weld integrity (welded spiral vane solid rigid, slip on welded positive), and appropriate coatings. Heavy duty options exist for demanding conditions.
- Deviated wells need specialized solutions: Spiralizers and roller centralizers are often preferred in highly deviated and horizontal wells to manage drag, torque, and ensure adequate cement coverage.
- Standoff bands offer simple support: Use stand off bands for basic standoff requirements or in tight tolerance situations.
- Procurement requires diligence: Focus on material specs, weld quality, design suitability, supplier reliability, communication, and overall value, not just price. Check for components like Self-drilling Hollow Anchors if your project involves broader ground support needs.
Choosing the right centralizer is a critical step in ensuring the success and longevity of your drilling projects. Understanding the different types and their specific applications allows for informed decisions that optimize performance and minimize risk.
Post time: 3 月-31-2025