Running casing successfully and achieving a perfect cement job are critical steps in well construction and other applications involving pipes or tubing in boreholes. A key component ensuring success is the centralizer. This article dives deep into the world of centralizer tools, exploring bow spring centralizer types, rigid centralizer options, and the versatile semi-rigid centralizer. We'll look at hinged non welded designs versus welded ones, understand the importance of restoring force and standoff, and help you choose the right tool for your specific needs, whether it's for vertical, deviated, or horizontal applications. Reading this will give you the confidence to select and utilize centralizers effectively, ensuring the integrity and longevity of your casing installations and cement operations.
ihong
1. What Exactly is a Casing Centralizer and Why is it Crucial?
A casing centralizer is a mechanical device secured around a casing pipe or tubing string. Its primary job is simple but vital: to keep the casing centered within the wellbore or borehole as it's being run in and during the subsequent cementing process. Think of it like bumpers keeping a car perfectly in the middle of a lane. By maintaining this central position, centralizers ensure that a uniform annular space (the gap between the casing and the borehole wall) is present all around the pipe.
This consistent annular space is absolutely essential for a successful primary cement job. Good centralization allows the liquid cement slurry to flow evenly around the entire circumference of the casing pipe, displacing drilling mud effectively and creating a complete, uniform cement sheath. A strong cement sheath provides zonal isolation (preventing fluid migration between different geological formations), supports the casing string structurally, and protects the casing from corrosion. Without proper centralization using a reliable centralizer, the casing can lie against one side of the borehole, leading to channeling (where mud isn't fully displaced), poor cement bonding, and potential well integrity issues down the line. Therefore, the humble centralizer plays a massive role in the long-term safety and productivity of a well or the stability of a ground anchor installation.
2. How Do Bow Spring Centralizers Work Their Magic?
The bow spring centralizer is perhaps the most common type you'll encounter. Its design relies on flexible, arched metal strips called bow springs. These bows are attached, often through welding or mechanical means, to end collars that fit around the casing pipe. As the casing string with the attached bow spring centralizer is lowered into the wellbore, the flexible bows compress against the borehole wall. This compression generates an outward-pushing force known as the restoring force.
It's this restoring force that actively pushes the casing away from the borehole wall, striving to keep it centered. The effectiveness of a bow spring centralizer is largely determined by its ability to generate sufficient restoring force under various downhole conditions, including deviations and tight spots. The flexibility of the bow spring design allows these centralizers to navigate through borehole irregularities and varying diameters more easily than their rigid counterparts, while still providing the necessary centering capability, often referred to as standoff (the percentage of the annulus where the casing is kept away from the wall). They are designed to provide positive standoff even when compressed.
3. What are the Key Features of a Standard Bow Spring Centralizer?
Standard bow spring centralizers come in various designs, but they share common features. The core components are the bow springs themselves and the end collars (or bands) that hold them. These bows are typically made from high-quality spring steel, heat-treated to achieve specific spring characteristics and ensure they can withstand repeated flexing without permanent deformation. The number, height (bow heights), and shape of the bows can vary depending on the casing size, hole size, and required restoring force.
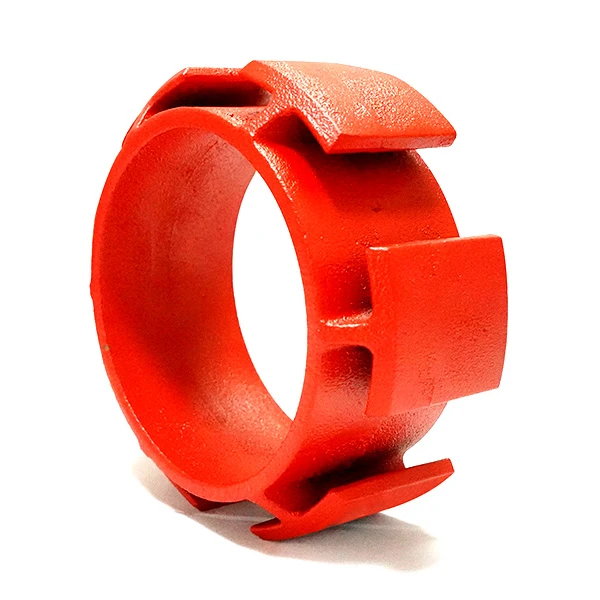
Construction methods differ, primarily between welded and non-welded types.
- Welded Bow Spring Centralizers: In these designs, the bow springs are directly welded onto the end collars. This often results in a very robust and economical centralizer.
- Non-Welded Bow Spring Centralizers: These centralizers utilize mechanical locking mechanisms, often involving interlocking tabs or channels on the bows and collars. Hinged non welded designs are particularly popular. These consist of two assembled halves connected by a hinge pin on one side and a locking mechanism on the other. This allows the centralizer to be easily installed over the casing pipe at any point on the rig floor, without needing to slide it over the end. This hinge design significantly simplifies installation, especially on longer casing strings. Many non-welded designs offer high restoring force capabilities. Both slip-on (requiring sliding over the casing end) and hinged (clamp-on) versions are available in welded and non-welded styles.
4. When Should You Choose a Rigid Centralizer for Maximum Standoff?
While bow spring centralizers offer flexibility, there are situations where maximum standoff and robustness are paramount, particularly in highly deviated or horizontal wells. This is where the rigid centralizer comes into play. Unlike bow spring types, a rigid centralizer does not rely on flexible bows. Instead, it features fixed blades or rollers integrated into a solid body. These blades directly contact the wellbore wall.
The primary advantage of a rigid centralizer is its ability to provide guaranteed standoff, often approaching 100%, regardless of side forces. Because the blades are fixed and non-flexible, the centralizer maintains the casing pipe at a set distance from the borehole wall. This makes them ideal for horizontal wells or highly deviated well sections where gravity pulls the casing strongly towards the low side of the hole. A rigid centralizer can withstand significant high side loads without collapsing like a bow spring might under extreme conditions. They are often made from cast iron, steel, or durable polymers. However, their rigidity means they have zero starting force (the force needed to insert the centralizer into the hole) beyond simple friction and can potentially get stuck in under-gauge sections or tight spots. Careful wellbore conditioning is often required when running rigid centralizers.
5. Understanding Semi-Rigid Centralizers: The Best of Both Worlds?
Recognizing the limitations of both purely flexible bow spring centralizers and completely rigid centralizers, the industry developed semi-rigid centralizers. These innovative tools aim to provide a balance, combining the features of both types. A semi-rigid centralizer typically uses bows that are significantly stronger and less flexible than those found on a standard bow spring centralizer, but not entirely inflexible like the blades of a rigid centralizer.
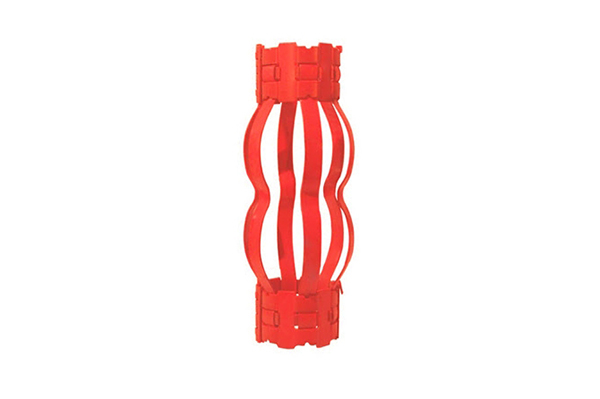
The goal of the semi-rigid centralizer (or semi rigid centralizer) is to offer a higher restoring force and better standoff capability than standard bow spring types, especially in deviated holes, while still retaining some flexibility to navigate minor borehole irregularities and potentially reduce the high starting force associated with purely rigid designs. They represent a middle ground, providing enhanced performance for more demanding applications without the absolute rigidity that might cause issues in less-than-perfect boreholes. This makes the semi-rigid design a popular choice for moderately deviated wells or situations requiring better-than-standard standoff.
6. What Makes Semi-Rigid Bow Spring Centralizers Unique for Challenging Wells?
The semi-rigid bow spring centralizer is a specific and highly effective category within the semi-rigid family. These centralizers are designed to excel in challenging well conditions, particularly deviated and horizontal wells. They achieve this by using extremely strong, specially heat-treated bow springs, often made from special alloy steel, which provide a significantly high restoring force. This ensures excellent standoff even when significant side forces are pushing the casing off-center. Many designs feature a double-crested profile on the bows, further enhancing their strength and restoring force.
A key characteristic of many high-quality semi-rigid bow spring centralizers is their combination of high restoring force with a relatively low starting force. This means they provide strong centering power downhole but are easier to run into the well compared to fully rigid centralizers. Many are available in hinged non welded configurations, making installation quick and secure using self-locking mechanisms. The semi rigid bow design ensures high efficiency in casing jobs on deviated and horizontal sections. For optimal performance, we often recommend installing semi-rigid centralizers over a stop collar to ensure they remain precisely positioned on the casing pipe. These centralizers provide superior performance where standard bow spring types might struggle. The semi-rigid bow spring centralizer is engineered for reliability in tough casing jobs. Some even feature a double bow configuration for added strength.
7. Hinged vs. Welded Centralizers: Which Construction is Better?
The choice between hinged (usually non-welded) and welded centralizers often comes down to operational preferences, cost, and specific application requirements.
-
Welded Centralizers:
- Pros: Often more economical due to simpler manufacturing. The weld points can create a very strong, integrated unit. Available in both slip-on and, less commonly, pre-assembled latch-on styles.
- Cons: Slip-on welded centralizers must be slid over the end of the casing pipe, which can slow down operations. The weld points can sometimes be points of stress concentration or potential corrosion if not properly coated (e.g., with iron phosphate and powder coating). Quality control of the weld is critical.
-
Hinged Non-Welded Centralizers:
- Pros: The primary advantage is ease and speed of installation. The hinge allows the centralizer to be opened and clamped around the casing at any location, drastically reducing handling time. This hinged non welded design avoids potential heat-affected zones associated with welding. Often designed for high performance with excellent restoring force. The end collar hinge is typically robust, and locking mechanisms are designed for secure closure.
- Cons: Can sometimes be slightly more expensive due to the more complex manufacturing involving the hinge and locking mechanism. The integrity of the hinge pin and locking device is crucial for performance.
Ultimately, both welded and hinged non-welded centralizers can perform excellently if manufactured to high standards (like API 10D specifications). The hinged non welded design often provides significant operational advantages, particularly for semi-rigid bow spring centralizers used in demanding casing runs.
8. Why is Proper Centralizer Placement So Vital for Effective Cementing?
Achieving a good cement job is arguably the most critical factor for well integrity, and centralizer placement is the foundation for good cementing. As mentioned earlier, centralizers create the necessary standoff, ensuring a consistent annular space around the casing pipe. This annular space is the pathway for the cement slurry. If the casing is lying against the borehole wall (poor standoff), the cement cannot flow into that narrow gap.
Proper placement means using the right type of centralizer and the right number of them, spaced correctly along the casing pipe string. Engineering software is often used to model the casing string and determine the optimal placement strategy based on well trajectory, casing properties, and centralizer performance (restoring force). When cement is pumped down the casing and up the annulus, adequate standoff allows the cement to completely displace the drilling mud from all sides of the pipe. This results in:
- Uniform Cement Sheath: Provides consistent structural support.
- Effective Zonal Isolation: Prevents fluids from flowing vertically behind the casing.
- Complete Mud Removal: Reduces the risk of corrosion and ensures a strong bond between the cement, casing, and formation.
- Prevention of Cement Channeling: Ensures the entire annulus is filled.
Without adequate standoff provided by correctly placed centralizers, the cement job can be compromised, potentially leading to costly remedial work or long-term well integrity problems. Using quality casing accessories like centralizers and Coupling devices is paramount.
9. What Factors Influence Centralizer Selection (API Standards, Hole Conditions)?
Selecting the appropriate centralizer isn't a one-size-fits-all decision. Several factors must be considered to ensure optimal performance and a successful casing and cementing operation:
- Well Trajectory:
- Vertical Wells: Standard bow spring centralizers often suffice.
- Deviated Wells: Semi-rigid or high-performance bow spring centralizers are usually needed due to increased side forces.
- Horizontal Wells: Rigid or robust semi-rigid centralizers are typically required to handle the high gravitational forces pulling the casing down.
- Hole Condition:
- Gauge Hole: Most centralizer types will perform well.
- Irregularities/Washouts: Bow spring or semi-rigid centralizers offer more flexibility to navigate varying diameters.
- Tight Spots/Doglegs: Flexible bow spring types or semi-rigid designs with low starting force are preferred over fully rigid centralizers to avoid getting stuck.
- Casing and Hole Size: The centralizer must be correctly sized for the specific casing OD (Outer Diameter) and the nominal/drift ID (Inner Diameter) of the open hole or previous casing. Manufacturers provide sizing charts.
- API Specifications (API 10D): The American Petroleum Institute sets standards for centralizer testing, defining parameters like Starting Force, Restoring Force, and Running Force. Choosing centralizers that meet or exceed API requirements provides quality assurance. Different classes within the spec relate to different levels of restoring force.
- Standoff Requirements: The desired standoff percentage (often targeted above 67% or 80%) influences the type and number of centralizers needed. Higher standoff usually requires more robust (rigid or semi-rigid) or a higher density of centralizers.
- Fluid Properties: The density and viscosity of drilling mud and cement slurry can affect the forces acting on the centralizers.
- Budget vs. Risk: While cost is a factor, selecting cheaper, lower-performance centralizers for demanding applications can lead to costly failures. The selection should balance cost with the technical requirements and potential risks of a poor cement job. Manufacturers often offer a wide range of bow heights and shapes enabling the customer to make an optimum choice matching their requirements.
10. How Can I Ensure Optimal Performance from My Bow Spring and Rigid Centralizers?
Getting the best performance from your chosen centralizers involves more than just selecting the right type. Proper handling, installation, and planning are crucial.
- Quality Control: Always source centralizers from reputable manufacturers who adhere to recognized standards like API 10D. Inspect centralizers upon arrival for any damage during shipping or manufacturing defects, especially checking weld integrity or hinge/locking mechanisms.
- Correct Installation:
- Ensure the centralizer is the correct size for the casing.
- For hinged centralizers, ensure the hinge pins are secure and the locking mechanism engages fully.
- For slip-on centralizers, slide them carefully onto the casing.
- Most importantly: Use Stop Collars! Centralizers (especially bow spring and semi-rigid types) should generally be installed between stop collars. These devices clamp onto the casing pipe and prevent the centralizer from sliding along the casing during run-in or cementing. This ensures the centralizer stays exactly where the engineers planned for it to be. We strongly recommend installing semi-rigid centralizers over a stop collar.
- Handling: Avoid rough handling that could damage the bows or structure of the centralizer. Don't stack heavy items on top of stored centralizers.
- Planning: Use appropriate software or consult expert recommendations for determining the correct number and spacing of centralizers for your specific well path and conditions to attain higher stand-off.
- Wellbore Conditioning: Ensure the borehole is as clean and smooth as possible before running casing. This minimizes the risk of any centralizer type getting stuck, especially rigid centralizers.
- Running Speed: Run the casing string at a controlled speed to minimize shock loading on the centralizers.
If you have specific requirements, challenging conditions, or need special sizes, don't hesitate to contact us. As manufacturers, we can provide guidance and potentially customized solutions, including various Nut and Bolt options for assembly if needed, to ensure you get the best possible performance from your centralizer program.
Key Takeaways:
- Centralizers are essential for centering casing in the wellbore, crucial for effective cementing.
- Bow Spring Centralizers offer flexibility and are suitable for many applications, generating restoring force via flexible bows.
- Rigid Centralizers provide maximum, guaranteed standoff, ideal for horizontal and highly deviated wells, but lack flexibility.
- Semi-Rigid Centralizers (including semi-rigid bow spring centralizers) balance strength and flexibility, offering high restoring force with manageable starting force, suitable for challenging wells.
- Hinged Non-Welded designs offer significant installation advantages over welded slip-on types.
- Proper centralizer selection depends on well trajectory, hole condition, size, API standards, and required standoff.
- Correct installation, especially the use of stop collars, is vital for ensuring centralizers perform as designed.
- Good centralization leads to better mud displacement, uniform cement sheaths, effective zonal isolation, and long-term well integrity.
Post time: 3 月-28-2025