Have you ever wondered how tunnels are built, mountains are mined, or even how the foundations for our buildings are laid? The answer often lies in the powerful capabilities of rock drills. These essential tools, whether pneumatic or hydraulic, are the workhorses of countless industries. This article will delve into the fascinating world of drills, exploring the various types of rock drills available and what makes each one uniquely suited for different tasks. Understanding the nuances of rock drills can be the key to efficiency and success in your projects, so let's drill down into the details!
Unveiling the World of Rock Drills: Your Comprehensive Guide
Rock drills are indispensable tools in various industries, from mining and construction to quarrying and even oil and gas. Choosing the right drill for the job is crucial for efficiency, safety, and cost-effectiveness. This article will explore the different types of rock drills, their functionalities, and their ideal applications. Whether you're involved in rock excavation, rock blasting, or simply curious about these powerful machines, this guide will provide valuable insights.
Deep Dive into Rock Drilling: Exploring the Mechanics and Applications
Let's delve into the specifics of drills and understand their vital role.
What is a Rock Drill and Why is it Important in Various Industries?
A rock drill, at its core, is a powerful tool used for making holes in rock. Its importance spans numerous sectors. In mining, rock drills are used extensively to create blast holes for rock blasting and for extracting valuable resources in underground mine operations. The efficiency of mining operations heavily relies on the performance of these drills. In construction, drills are essential for foundation work, tunneling, and road construction, where breaking through solid rock formations is often necessary. Even in the oil and gas industry, specialized drills are designed to penetrate deep into the earth. The fundamental principle involves applying force to a drill bit to fracture the rock face. Whether it's a pneumatic rock drill powered by compressed air or a hydraulic rock drill driven by fluid pressure, the result is the same: creating precise drill holes.
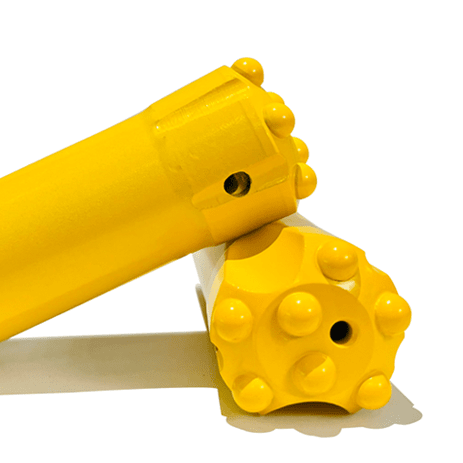
The impact of rock drill technology on human progress is undeniable. Consider the vast infrastructure projects that wouldn't be possible without them. From subway systems burrowing beneath cities to dams harnessing the power of rivers, drills are the unsung heroes. Even seemingly smaller tasks, like quarrying stone for building materials, depend on the efficiency and power of these tools. The development of more efficient and powerful drills directly translates to faster project completion times and reduced costs. Furthermore, advancements in rock drill technology have also led to safer working conditions, particularly in hazardous environments like underground mining.
What are the Key Components of a Typical Rock Drill?
While the specific design may vary between different types of rock drills, some core components are common. The drill bit is the cutting element that comes into direct contact with the rock. The drill rod, or sometimes referred to as drill pipe, transmits the force from the drill mechanism to the drill bit. In many drills, a piston is a crucial part, delivering repeated impacts to the drill rod. The backhead of the drill houses the controls and connections for the power source, be it compressed air for a pneumatic model or hydraulic fluid for a hydraulic drill. The system that feeds the drill forward, applying the necessary pressure against the rock, is also a vital component. In larger operations, the drill is often mounted on a drill rig for stability and maneuverability. Understanding these components helps in troubleshooting and maintaining the drilling equipment.
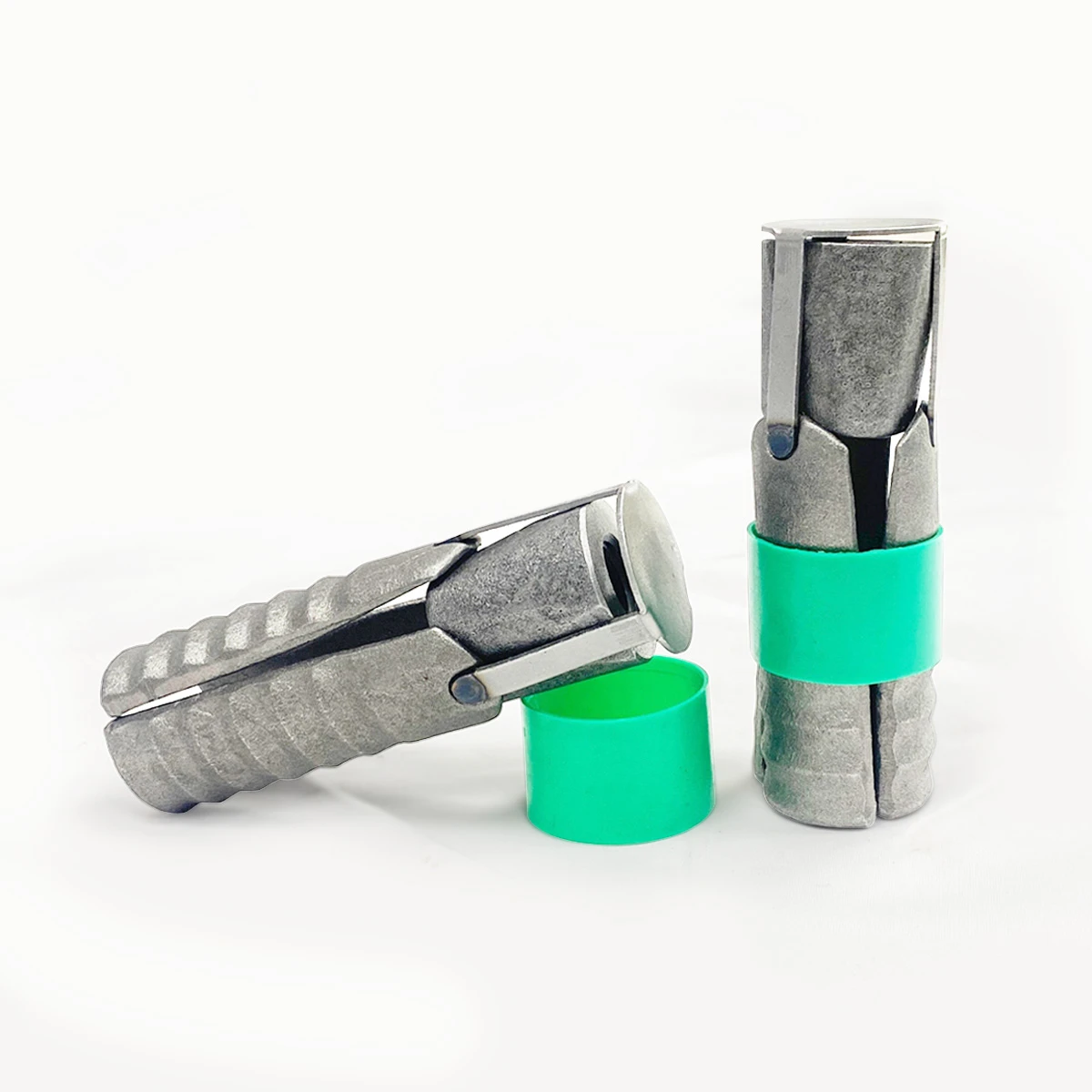
The way these components interact determines the drilling action. For example, in a pneumatic rock drill, compressed air drives the piston, which in turn strikes the rock via the drill rod. The drill bit is rotated to ensure even wear and efficient cutting. In a hydraulic rock drill, hydraulic fluid under high pressure powers the piston. Lubrication systems are also essential to reduce friction and wear on moving parts, extending the lifespan of the drill. Furthermore, systems for removing drill cuttings from the drill hole are integrated into many modern rock drill designs. These systems can use air or water to flush out the debris, preventing it from interfering with the drilling speed and efficiency. The quality and durability of each component directly impact the overall performance and reliability of the rock drill. You might find similar principles in the operation of a Self-drilling Hollow Anchor which also relies on impact and rotation for penetration.
Pneumatic Rock Drill vs. Hydraulic Rock Drill: Which One is Right for Your Needs?
The choice between a pneumatic rock drill and a hydraulic rock drill often boils down to the specific requirements of the job. Pneumatic drills, powered by compressed air, are generally lighter and more portable. They are a common sight in construction sites and smaller mining operations. The simplicity of their design makes them relatively easy to maintain. However, their power output might be limited compared to their hydraulic counterparts. Hydraulic rock drills, on the other hand, deliver significantly higher power and are better suited for drilling harder types of rock and larger diameter drill holes. They are frequently used in large-scale mining operations and major construction projects requiring substantial rock excavation.
The operational considerations also differ. Pneumatic drills require a reliable source of compressed air, usually from a compressor. The efficiency of pneumatic drills can be affected by air pressure fluctuations and potential leaks in the air lines. Hydraulic drills require a hydraulic power unit and are generally more energy-efficient for high-power applications. However, they are typically heavier and more complex, potentially requiring specialized maintenance. The noise levels also vary; pneumatic drills tend to be noisier than hydraulic drills. For tasks requiring precision and high power in demanding conditions, hydraulic rock drills often emerge as the preferred choice. Think of large tunnel boring machines or the powerful drills used in open-pit mining. Conversely, for smaller, more mobile applications, pneumatic drills offer a practical and cost-effective solution. The decision often mirrors the considerations when choosing between different types of Bolt – the application dictates the best option.
What are the Different Types of Rock Drills Based on Their Mechanism?
Beyond the power source, types of rock drills can be categorized by their drilling mechanism. Top hammer drills are a common type where the hammer drill mechanism is located at the top of the drill string, striking the drill rod directly. This impact energy is transmitted down the drill string to the drill bit, which crushes the rock. DTH drills (Down-The-Hole drills) have the hammer drill mechanism located directly behind the drill bit at the bottom of the hole. This provides a more direct transfer of energy and is particularly effective for drilling deeper drill holes and harder types of rock. Rotary drills rely on continuous rotation and downward pressure to grind away the rock, often using drilling by use of cutters. Rotary percussive drilling combines both rotation and percussive (hammering) action for increased efficiency in certain rock formations.
Each mechanism has its strengths and weaknesses. Top hammer drills are versatile and widely used in construction and quarrying. DTH drills excel in deeper hole drilling and are frequently employed in mining and water well drilling. Rotary drills are effective in softer rock and are often used in oil and gas drilling. The choice of mechanism also impacts the drill string and drill bit design. For instance, DTH drills typically use shorter, more robust drill rods compared to the longer drill rods used in top hammer drills. Understanding the underlying mechanics is crucial for selecting the optimal drill for a specific geological condition and drilling objective. Even within the realm of self-drilling technology, as seen in a Self-drilling Hollow Anchor, the principles of impact and rotation are fundamental.
How Does Rock Strength Influence the Choice of Rock Drill?
The rock strength, or the resistance of the rock to fracturing, is a primary factor in determining the most suitable rock drill. For softer types of rock, a less powerful drill, such as a smaller pneumatic model or a rotary drill, might suffice. However, when dealing with hard rock formations like granite or basalt, more powerful drills are necessary. Hydraulic rock drills and DTH drills are often preferred for their ability to deliver high impact energy. The choice of drill bit also becomes critical. For hard rock, drill bits with tougher materials and more aggressive cutting structures are required. Understanding the compressive strength and abrasiveness of the rock is essential for optimizing drilling speed and minimizing wear and tear on the drilling equipment.
Consider the challenges of percussive drilling of quartzite, a very hard and abrasive rock. In such scenarios, high-powered hydraulic drills with specialized drill bits featuring cemented carbides in rock drilling are essential. Conversely, drilling in soft rock like sandstone or shale might be efficiently handled by lighter pneumatic drills or rotary drills. Geological surveys and rock testing are crucial steps before embarking on any drilling project to accurately assess the rock strength. Failing to consider this factor can lead to inefficient drilling, premature equipment failure, and increased project costs. The selection process often involves analyzing samples of the rock and consulting geological data to determine the optimal drilling parameters and equipment. This careful consideration of rock strength is as important as choosing the right type of Washer for a secure fastening.
What are the Advantages and Disadvantages of Using Pneumatic Rock Drills?
Pneumatic rock drills offer several advantages. Their relatively simple design makes them more affordable to purchase and maintain. Their lighter weight enhances portability, making them suitable for applications where maneuverability is key. They are also generally easier to operate, requiring less specialized training. However, pneumatic drills also have limitations. Their power output is typically lower compared to hydraulic drills, making them less efficient for very hard rock. The need for a compressed air supply can be a logistical constraint, and the efficiency of the drill can be affected by pressure fluctuations and leaks. Noise levels are also a common concern with pneumatic drills.
Despite these disadvantages, pneumatic drills remain a workhorse in many industries. Their simplicity and portability make them ideal for smaller construction projects, demolition work, and secondary breaking of oversized rocks in quarries. The initial investment cost is lower, which can be a significant factor for smaller businesses. Regular maintenance, including checking air lines for leaks and ensuring proper lubrication, is crucial for maximizing the lifespan and performance of pneumatic drills. The development of quieter and more efficient pneumatic models continues to address some of their traditional drawbacks. Just like choosing the right Nut for a specific bolt, selecting a pneumatic drill requires understanding its capabilities and limitations in the context of the task at hand.
In What Scenarios are Hydraulic Rock Drills the Preferred Choice?
Hydraulic rock drills shine in scenarios demanding high power and efficiency. They are the go-to choice for large-scale mining operations, major tunneling projects, and any application involving hard rock formations. Their ability to deliver consistent high power translates to faster drilling speed and greater productivity. Hydraulic drills also tend to be more energy-efficient for high-power applications compared to pneumatic drills. Furthermore, they often operate at lower noise levels, contributing to a better working environment.
The robust construction and powerful performance of hydraulic drills make them indispensable for tackling challenging geological conditions. When drilling deep drill holes or working with highly abrasive rock, the durability and power of hydraulic drills are essential. Modern hydraulic drill systems often incorporate sophisticated controls and monitoring systems, allowing for precise adjustments and optimizing drilling parameters. While the initial investment and maintenance costs might be higher, the increased productivity and efficiency often outweigh these factors in demanding applications. The power and precision of a hydraulic rock drill are akin to the strength and reliability required in applications using Diamond Mesh for reinforcement.
Are Electric Rock Drills a Viable Alternative for Certain Applications?
Electric rock drills are gaining traction as a viable alternative, particularly in applications where environmental concerns and noise reduction are priorities. They eliminate the need for compressed air or hydraulic fluid, offering a cleaner and potentially quieter operation. Advancements in battery technology are also making cordless electric rock drills more powerful and practical for certain tasks. While they might not yet match the raw power of large hydraulic drills, electric rock drills are well-suited for smaller construction and demolition jobs, as well as underground applications where ventilation is a concern.
The benefits of electric rock drills extend beyond environmental impact. They often require less maintenance compared to pneumatic or hydraulic models, and the absence of air hoses or hydraulic lines improves safety and reduces trip hazards. The portability of cordless models offers added convenience. However, the power output and battery life are still considerations for heavy-duty applications. Ongoing development in battery technology and motor efficiency is continuously expanding the capabilities of electric rock drills, making them an increasingly attractive option for a wider range of drilling tasks. Their precision and cleaner operation can be compared to the careful application required when using Butyl Tape for sealing.
What Role Does the Drill Bit Play in the Effectiveness of a Rock Drill?
The drill bit is the crucial interface between the drill and the rock. Its design, material, and condition directly impact the drilling speed, efficiency, and the quality of the drill hole. Different types of rock drills require specific drill bit designs. For percussive drilling, drill bits with tungsten carbide inserts are common, designed to withstand repeated impacts. For rotary drilling, drill bits with cutting edges or buttons made of hard materials like diamond or tungsten carbide are used. The size and shape of the drill bit are determined by the desired drill hole diameter and the type of rock being drilled.
Maintaining sharp and effective drill bits is paramount. Worn or damaged drill bits significantly reduce drilling speed, increase energy consumption, and can even damage the drill. Regular inspection and timely replacement of drill bits are essential for optimizing performance. The selection of the correct drill bit for the specific rock strength and drilling application is just as important as choosing the right rock drill itself. Innovations in drill bit technology, such as improved carbide grades and cutting geometries, are constantly pushing the boundaries of drilling efficiency. The precision engineering of a drill bit is comparable to the accuracy required in using a Measuring Rope for precise measurements.
Looking Towards the Future: What are the Latest Advancements in Rock Drill Technology?
The field of rock drill technology is constantly evolving. Current advancements focus on increasing efficiency, reducing environmental impact, and enhancing safety. Developments in automation and remote control are leading to more autonomous drilling operations, particularly in hazardous environments. Improved sensor technology allows for real-time monitoring of drilling parameters, optimizing performance and preventing equipment damage. Research into new materials for drill bits and drill rods aims to improve durability and drilling speed. The integration of digital technologies and data analytics is also playing a growing role in optimizing drilling operations and predictive maintenance.
Manufacturers are increasingly focusing on developing quieter and more energy-efficient drills. The adoption of electric and hybrid power systems is gaining momentum, driven by environmental concerns. Furthermore, advancements in dust suppression technology are improving air quality in drilling environments, enhancing worker safety. The future of rock drilling promises more intelligent, efficient, and sustainable solutions, driven by innovation and a commitment to safety and environmental responsibility.
- Rock drills are essential tools in numerous industries.
- Different types of rock drills are suited for different applications and rock strength.
- Pneumatic drills offer portability, while hydraulic drills provide high power.
- The drill bit is a critical component affecting drilling efficiency.
- Advancements in technology are making rock drills more efficient, safer, and environmentally friendly.
Post time: 1 月-08-2025